How to Use Plywood for Curved Concrete Forms
Plywood is a versatile material that can be used for various construction projects, including creating curved concrete forms. By understanding the basics of plywood and concrete forms, as well as knowing how to prepare the plywood and assemble the form, you can successfully use plywood for curved concrete forms. In this article, we will walk you through the process step by step.
Understanding Plywood and Concrete Forms
Before diving into the specifics of using plywood for curved concrete forms, it’s essential to have a solid understanding of the properties of plywood and the role of concrete forms.
By following these steps, you can effectively use plywood curved concrete forms. Remember to choose the right plywood, prepare it correctly, and assemble the form with precision. With practice and attention to detail, you can create beautiful curved concrete structures using plywood as your go-to material.
When it comes to plywood, it is crucial to consider not only the type of wood used but also the adhesive that binds the layers together. The most common types of plywood are made from hardwoods like birch or oak, which offer strength and durability. Additionally, the adhesive used in plywood production plays a significant role in its performance. Phenol formaldehyde and melamine formaldehyde adhesives are commonly used for exterior-grade plywood, providing water resistance and durability against the elements.
The Basics of Plywood
Plywood is made from thin layers of wood veneer that are glued together to create a strong and durable material. It comes in various thicknesses and grades, and the type of plywood you choose will depend on the requirements of your project.
Furthermore, the grading system for plywood, such as A, B, C, and D, indicates the quality of the material and any imperfections present. Grade A plywood has a smooth, sanded surface with minimal defects, making it ideal for projects where appearance is crucial. On the other hand, Grade D plywood may have knots, voids, and splits, making it suitable for structural applications where aesthetics are less important.
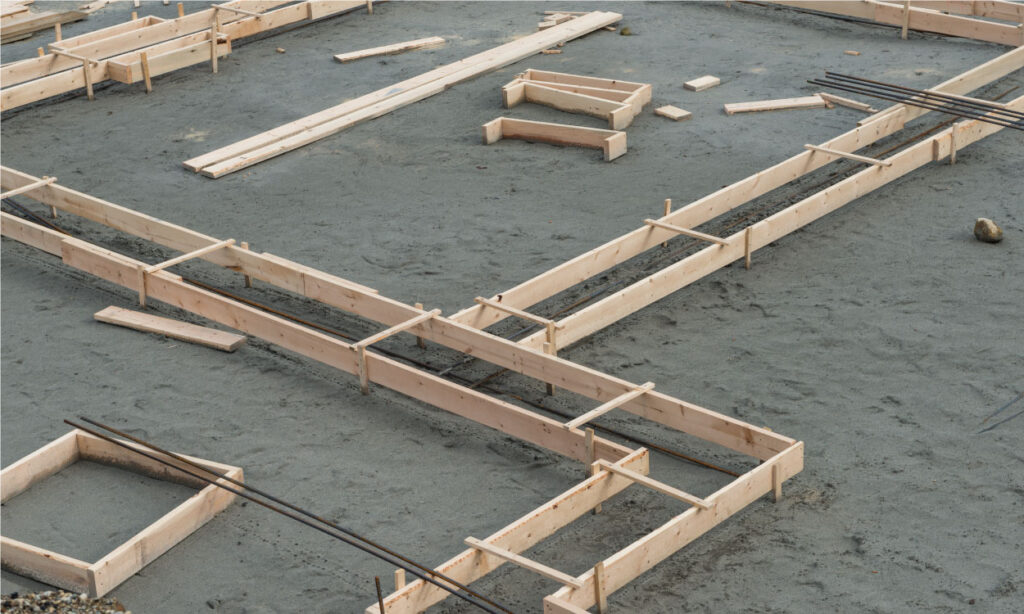
The Role of Concrete Forms
Concrete forms are temporary structures used to hold freshly poured concrete in place until it cures and hardens. They help create the desired shape and provide stability to the concrete during the pouring and setting process.
Moreover, concrete forms come in various materials, including plywood, metal, and plastic, each offering unique benefits. Plywood forms are popular due to their versatility, cost-effectiveness, and ease of use. They can be easily cut and shaped to accommodate different project requirements, making them ideal for curved or custom-shaped concrete elements. Additionally, plywood forms can be reused multiple times with proper care and maintenance, providing a sustainable solution for construction projects.
Read more on: Concrete Form Plywood
Necessary Materials for Curved Concrete Forms
Before starting your curved concrete form project, you will need to gather the necessary materials. These materials include the right plywood and additional tools and supplies.
Creating curved concrete forms can add a unique and visually appealing element to your construction project. The process requires attention to detail and the right materials to ensure a successful outcome.
Choosing the Right Plywood
When it comes to curved concrete forms, not all plywood is created equal. You need to select a plywood that is flexible enough to bend without breaking while retaining its structural integrity. One suitable option is ACX plywood, known for its durability and stability. Find more about integrity at https://ethicalleadership.nd.edu/news/what-is-integrity/
ACX plywood is a type of exterior-grade plywood that is commonly used in construction projects due to its strength and resistance to moisture. Its smooth surface allows for easy marking and cutting, making it ideal for creating precise curved forms for concrete.
Additional Tools and Supplies
In addition to plywood, you will need several other tools and supplies to complete your curved concrete form project. These may include a circular saw, measuring tape, pencil, clamps, and screws.
Having the right tools at your disposal is crucial for achieving accurate and professional results when working with curved concrete forms. The circular saw will help you cut the plywood to the desired shape, while the measuring tape and pencil are essential for marking out precise measurements. Clamps and screws will be necessary for securing the plywood in place as you form the curves.
Preparing the Plywood for Curved Forms
Once you have your materials ready, it’s time to prepare the plywood for bending and shaping. This involves measuring and cutting the plywood to the desired dimensions and employing bending techniques. Before you begin, it’s important to understand the properties of plywood and how it reacts to bending. Plywood is made up of thin layers of wood veneer that are glued together, providing strength and flexibility. When bending plywood, you need to consider the direction of the wood grain to ensure a successful curve without cracking.
Measuring and Cutting the Plywood
Start by measuring and marking the plywood according to the dimensions of your curved concrete form. Precision is key in this step to ensure a seamless fit when constructing the form. Use a circular saw with a fine-tooth blade to cut along the marked lines. Take your time to ensure accurate cuts, as any errors here can affect the overall quality of the form.
When cutting the plywood, be mindful of the blade’s position in relation to the wood grain. Cutting against the grain can result in splintering and rough edges, so it’s best to position the plywood to minimize tearout. Additionally, consider using a straight edge or clamps to guide the saw for straight and clean cuts.
Bending Techniques for Plywood
There are a few techniques you can use to bend plywood for curved forms. One method is to dampen the plywood with water, which softens the fibers and makes it more pliable. This technique is particularly effective for tight curves where flexibility is crucial. Another approach is to create a bending jig or form that matches the desired curve of the plywood. By clamping the plywood to the form and allowing it to set, you can achieve consistent and precise curves for your project.
Experiment with different bending techniques to find the one that works best for your specific project. Keep in mind that patience and practice are key when working with plywood, as mastering the art of bending takes time and skill. By understanding the characteristics of plywood and honing your bending techniques, you can create stunning curved forms that elevate your woodworking projects to the next level.
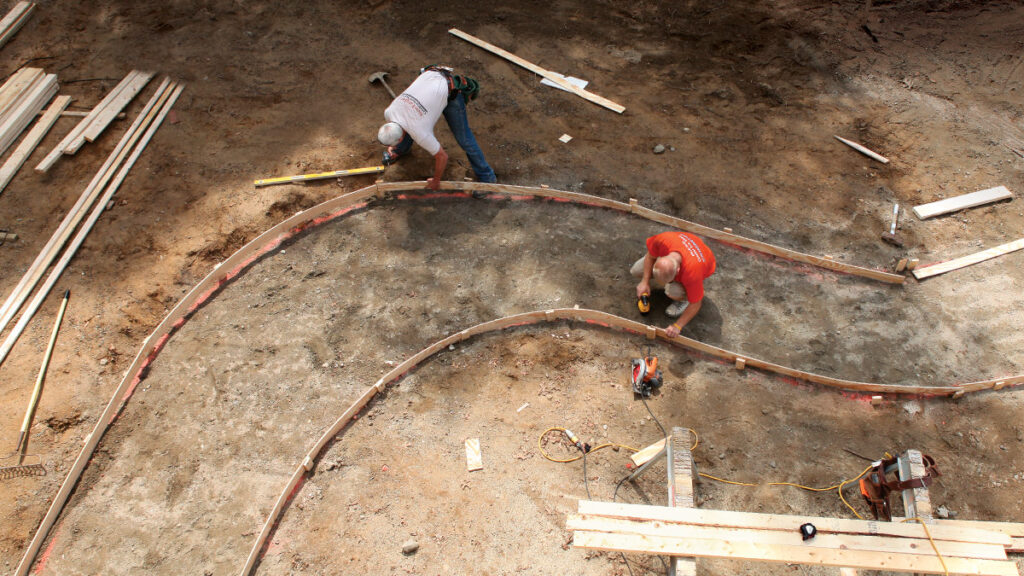
Assembling the Curved Concrete Form
With your plywood prepared, it’s time to assemble the curved concrete form. This involves securing the plywood and ensuring the correct curve for optimal concrete placement.
Before moving forward with the assembly process, it’s crucial to consider the environmental factors that may affect the concrete curing process. Factors such as temperature, humidity, and wind speed can all impact the final outcome of your concrete project. Taking these into account will help ensure a successful and durable result. Click here to learn more about temperature.
Securing the Plywood
Using clamps and screws, secure the bent plywood into position to create the curved form. Make sure the plywood is tightly fastened to maintain the desired shape and prevent any movement during the pouring and setting process.
Additionally, applying a release agent to the plywood surface can help prevent the concrete from sticking and make it easier to remove the form once the concrete has set. This simple step can save you time and effort during the demolding process.
Ensuring the Correct Curve
Double-check the curve of your form to ensure it matches the intended design. Take measurements and make adjustments as necessary to guarantee the correct shape before proceeding to the next step.
Consider using a flexible curve ruler or template to verify the accuracy of the curve and make any final tweaks before pouring the concrete. Attention to detail at this stage will contribute to a smooth and professional finish on your concrete project.
Pouring and Setting the Concrete
Now that your curved concrete form is ready, it’s time to pour and set the concrete. This process requires careful attention to detail to achieve desired results.
Before pouring the concrete, it’s crucial to ensure that all necessary safety precautions are in place. This includes wearing appropriate personal protective equipment such as gloves, goggles, and a mask to protect yourself from potential hazards. Additionally, make sure the work area is well-ventilated to prevent the inhalation of harmful fumes.
The Process of Pouring Concrete
Pour the concrete into the prepared form, making sure to distribute it evenly and avoid any air pockets. Use a shovel or rake to level the surface and smooth out any imperfections. Follow the specific instructions for the concrete mix you are using.
As you pour the concrete, it’s essential to work efficiently to prevent the mixture from drying out too quickly. Consider enlisting the help of a partner to ensure a smooth and continuous pouring process, especially when working with larger quantities of concrete.
Tips for Setting Concrete in Curved Forms
Setting concrete in curved forms requires extra care and precision. It’s important to continuously monitor the curing process and make any necessary adjustments to ensure the concrete maintains the desired shape. Make sure to follow the recommended curing time and consider using concrete additives for enhanced strength and durability.
After pouring the concrete, cover the form with a plastic sheet or damp burlap to regulate moisture evaporation and promote proper curing. This step is crucial in preventing cracks and ensuring the structural integrity of the concrete over time.